営業部塚田です。今月は弊社で行っている改善活動の一例をご紹介させて頂きます。 内容を簡単に申しますと、「元々マシニングで加工をしようとしていた箇所を、冶具を作成し旋盤で加工できるようにした」というもの。この改善により、工程数が4工程から1工程に減り、加工時間も30分程短縮したとのことです。言葉だけだと分かりにくいので、今回も図を用いてご説明↓
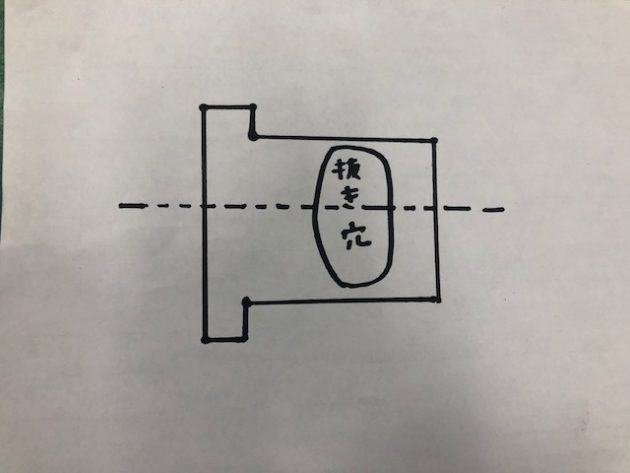
抜き穴 上記図は側面図だと思って頂ければと思います。図のように側面に抜き穴が4面、4か所に空ける加工があり、マシニングで加工をするには1面ごと乗せ換えをしながらやらなければなりませんでした。受注数も8ケあったのでこれでは加工時間も手間もかかってしまう。NCとマシニングの担当加工者はいい方法がないかを考え、冶具を製作すれば旋盤にて1発で加工ができるのでは?と気づきました。その時に製作した冶具がこちら↓
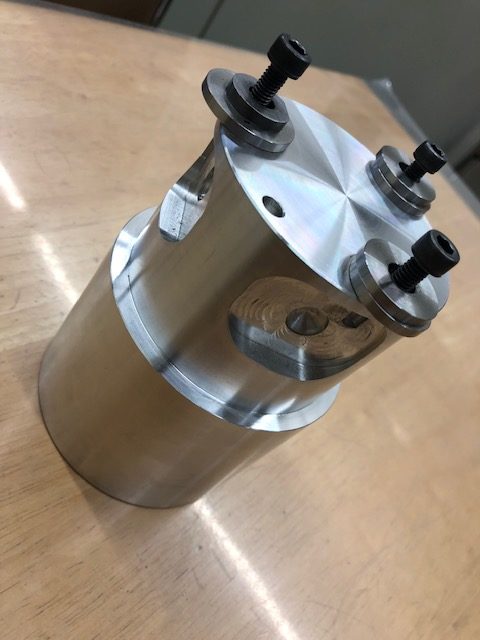
使い方のイメージとしてはこんな感じですかね。↓
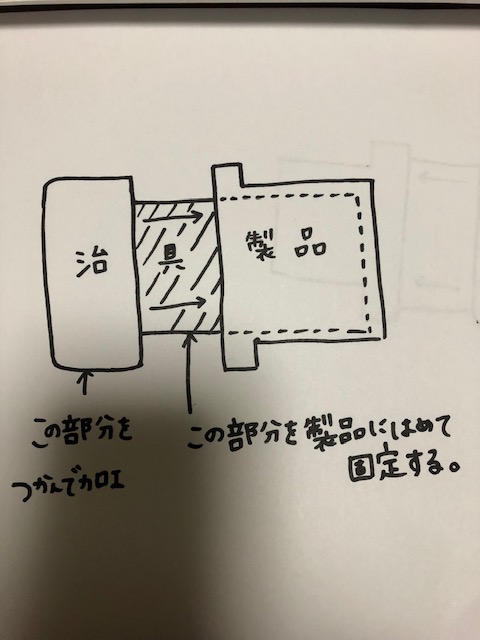
元々掴む場所が無かった為、旋盤では加工が出来なかった。ですが、冶具を作成し掴む場所を作ってあげたことで旋盤でも加工が出来るようになったという訳です。 今回のように加工時間が長くかかってしまうからしょうがない、どうしたら少しでも時間短縮になるのか?を考えたり、バリが出てしまうからしょうがない、ではなくいかに機械加工のみで綺麗な製品が出来るのか?等考えながら加工者達は日々改善をしています。また、それを1人で考えるのではなく今回のように部署の壁を越え、相談し合って加工に取り組んでおります。このような習慣を継続し、前回よりも今回・今回よりも次回とレベルアップした製品を製作していけたらと思います。